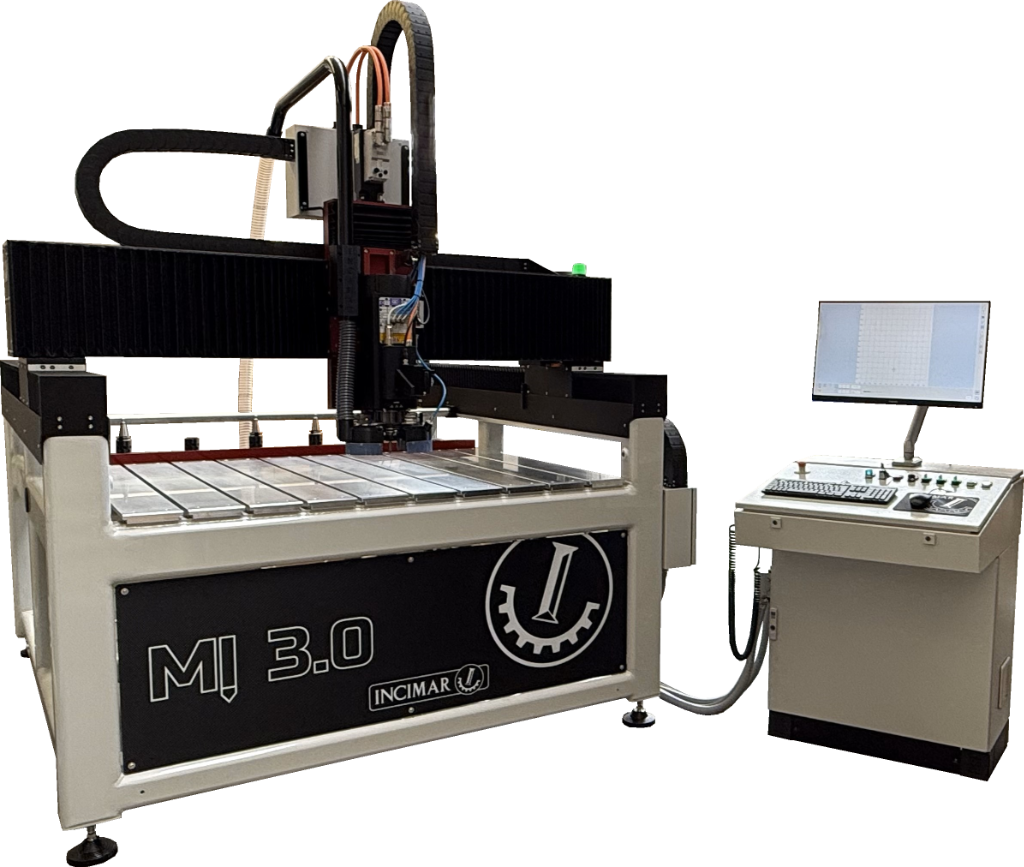
Dalla continua ricerca e innovazione nasce l’Incisografo MI 3.0, la piccola dalle grandi prestazioni.
Con un’area di lavoro di 1350x1200mm la MI 3.0 si presta ad incidere la maggior parte delle lastre, con la possibilità di incidere anche lastre più lunghe di 1350 facendole scorrere lateralmente sotto la struttura assi.
Highest quality machining, equipped with 3D laser acquisition sensor and tool calibration sensor, "small" in size but big in results.
Main Features:
- Work Area: 1350x1200mm
- Z-axis movement: 200mm
- Electrospindle with Internal Pressurization and ISO-30 cone seat
- 3D Acquisition Laser
- Tool Calibration Sensor
- Remote Control for Fine Positioning
- Tool Warehouse with 10 Workstations
- Software INCX
Electrical and Pneumatic Demands
Incisografo:
- Three-phase voltage 400 v - 5-pole 16A socket (3 phases + neutral + ground) for the machine body
- 7 Kw/h during operation, with 10 Kw/h peak
- 0.3mA delayed differential
- Dehumidified and filtered compressed air with pressure up to 7bar (6 for engaging and disengaging tools from the electrospindle)
Dust Extractor (optional):
- Three-phase voltage 400 v - 4-pole 16A socket (3 phases + ground) for vacuum cleaner
- 6 Kw/h for Dust Extractor
- 6 bar for Dust Extractor
-
The ISO 30 electrospindle, capable of up to 12,000 rpm and equipped with internal pressurization to safeguard the ball bearings from dust infiltration.
The electrospindle can also work with water tip cooling.
The machine uses brushless motors with integrated Ethercat drives.
This allows us to be able to monitor the correct operation of the machine at all times and to be able to take targeted action if problems occur.
The 3D capture laser is used both to acquire bas-reliefs or 3D models and to survey the surface of the plate to be engraved.
Once the surface is acquired, the machine will lay the engraving on it, thus enabling perfect execution even on uneven surfaces.
The calibration sensor is used just before execution to detect how much the tool protrudes from the ISO-30 taper.
With this information, the INCX software is able to correctly lay the tool on the plate surface for execution with perfect depth.
The CyberHead: a specially designed suction mouth to suck up the most dust during engraving and thus safeguard the cutting edge of the tool as much as possible.
The CyberHead can be opened by remote control to control execution in real time.
The CyberHead is also available for tool cooling with water nozzles.
Frequently Asked Questions
The difference is only in the size of the actual working area. While the MG has a working area of 2300x1200mm, the MI can engrave on an area of 1350x1200mm with the possibility of engraving even plates of a size larger by being able to insert it and slide it sideways.
The Engraver consists of three pieces of software: the machine control software, the Incimar composer, and the Aspire design program.
The course for the Incimar control software takes about 2 hours, for the Incimar composer 2 hours, and for the Aspire software 4 to 8 hours, depending on the customer's experience with cad/cam environments.
Incimar staff, however, is always available to intervene even by tele-assistance in case of doubts or problems.
The use of water, besides being wasteful, is highly overrated in the field of artistic engraving on marble, while it may make sense in engraving on materials such as granite or hard stone.
Our Engravers are set up to be able to adopt water cooling as well, but if most of the work is on marble or "soft" stones we can safely say that the use of water is not absolutely necessary and that the tool can safely engrave even large bas-reliefs without suffering.